Commercially viable circular-economy-based materials with properties similar to or better than their less sustainable equivalents could dramatically shrink the carbon footprint of the construction industry.
FFS industry partner EcoMag Ltd, keen to broaden the application of its hydrated magnesium carbonate/magnesium (di)hydroxide (HMC/MDH) product, saw an opportunity in developing sustainable construction materials.
To help it realise this opportunity, EcoMag teamed with chemical engineers at UNSW Sydney in an exciting FFS-backed project. The ‘Circular economy framework to manufacture sustainable construction materials from agri-food wastes’ (‘Agri-food waste CE framework’) project aims to develop and scale a new generation of building materials manufactured according to a circular-economy (CE) framework.
For the past year, the project team, led by UNSW Associate Professor Jason Scott, has been investigating the most efficient, sustainable way to create low-carbon construction materials by combining three waste streams: agricultural by-products; captured CO2 emissions; and HMC/MDH recovered from the waste bitterns of a solar salt-mining operation in Dampier, Western Australia.
The goal of the four-year project is to produce, at prototype scale, an environmentally sustainable, economically feasible, high-performance CE construction material that meets or exceeds current Australian and New Zealand Standards.
“Project success will deliver a blueprint for manufacturing new plasterboard materials that adheres to a circular economy framework, lowering their impact on the environment,” A/Prof. Scott says.
EcoMag CEO Tony Crimmins is excited about the project’s potential to realise the value of precious resources that would otherwise be lost to the system.
“What is becoming apparent is that waste is not the word we should be using to describe a resource that is discarded. It has negative connotations, and in this case, the discharged resource is a better product,” Crimmins contends. “Our plasterboard inherently has fire-retardant properties much in demand by the construction industry, and strength, attributed to the natural fibres of biochar.”
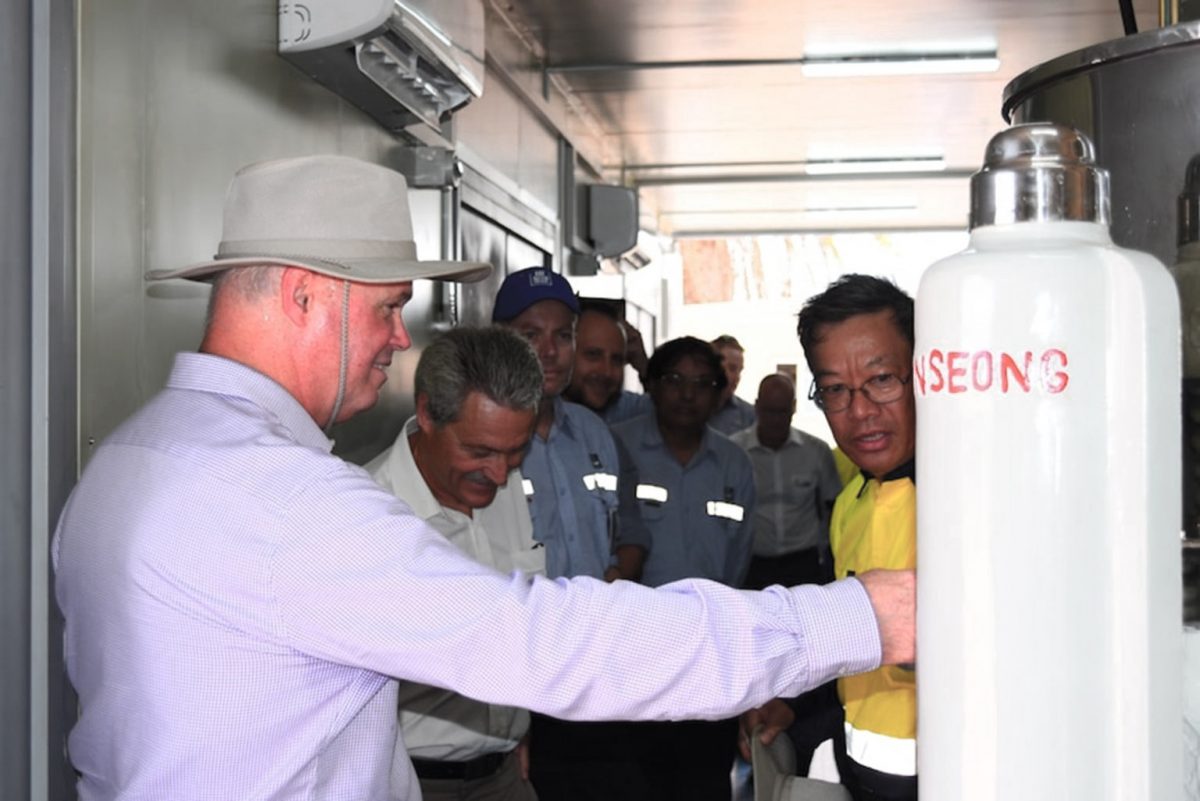
Tony Crimmins believes low-carbon products will be in big demand in the near future. Credit: EcoMag Ltd
Ensuring the new materials meet (or exceed) AS/NZS Standards
Materials considered by the project team were internal cladding (plasterboard), external cladding, concrete and bricks. “We narrowed that down to internal (plasterboard) and external cladding materials, as they represent cases where HMC/MDH is most readily adaptable and can potentially provide the greatest advantages in terms of properties (e.g., weight, moisture tolerance, fire retarding) compared to current commercial products (e.g., gypsum),” explains A/Prof. Scott.
The team then reviewed AS/NZS Standards for internal and external cladding and collated values for each Standards criterium to gain a complete appreciation of the key characteristics required in such materials – including their suitability for both sheet roof and wall cladding; strength (e.g., bending strength, edge hardness, bond strength); environmental tolerance (e.g., water resistance, humidified deflection, frost resistance, heat-rain, soak-dry, etc.) and fire-retarding capacity (e.g., smoke and growth rate, time to ignition, flammability, spread of flame, heat evolved, etc.).
“Interestingly, an ongoing review of the literature on internal drywall materials development has indicated that in most cases, the sole characteristic used to assess these materials is compressive strength,” says A/Prof. Scott. “As yet, we have found no research studies that also consider tensile strength, water resistance, flexibility or weathering of any newly developed materials.
“This suggests that there is a gap in the knowledge and that, in the past, a limited approach has been used to define the performance of internal drywall materials.”
“There’s thus an opportunity for us to produce new, better cladding based on a CE framework that not only meets, but exceeds the current AS/NZS Standards,” A/Prof. Scott says.
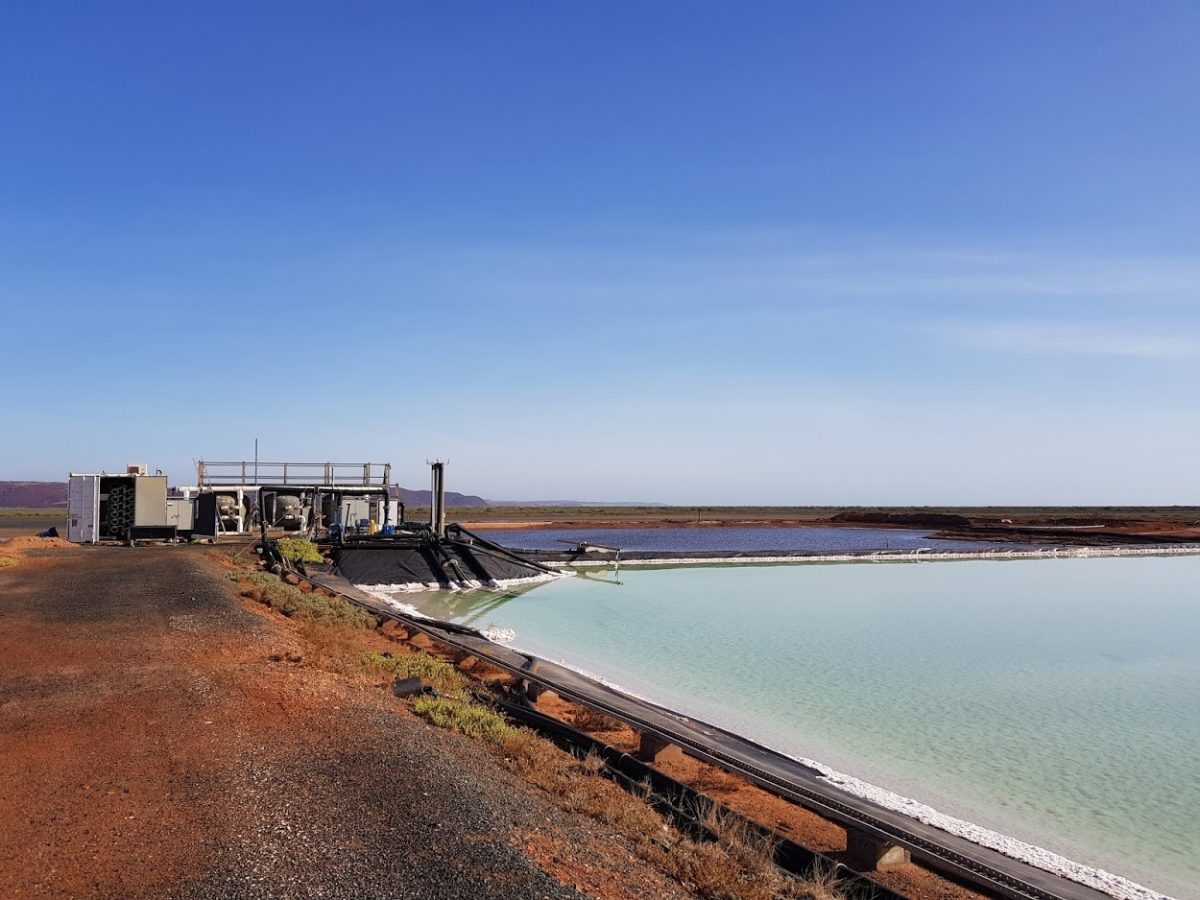
Sea-salt waste bittern in Dampier, WA. SME EcoMag Ltd is working with scientists within the UNSW’s Faculty of Engineering to scale up its process for turning high-grade magnesium, carbon recovered from industrial processes, and agricultural waste such as pine and straw, into sustainable low-carbon plasterboard for the construction industry. Credit: EcoMag Ltd
Assessing the sustainability and economic viability of the new CE manufacturing process
In the three months to 30 June, the project team undertook a life-cycle analysis (LGA) to ascertain the environmental gains that could be made by upcycling specific waste streams to into new-gen construction materials.
“The aim of the feasibility study was to assess the environmental footprint of high-purity HMC, MDH and magnesium oxide (MgO) recovered from the magnesium-rich bitterns in Dampier,” A/Prof. Scott explains.
“The analysis considered existing processes as well as future carbon-footprint improvements associated with carbon capture; feedstock switching, from Na2CO3 to NaOH; and fuel switching, from natural gas to electrified heat.
“The benefit of switching the feedstock to NaOH is it provides an opportunity to integrate carbon dioxide capture and utilisation within the EcoMag process, via the formation of Na2CO3 (Figure 1). EcoMag has now modified its pilot plant to integrate CO2 capture into the hydrated magnesium carbonate recovery process,” A/Prof. Scott says.
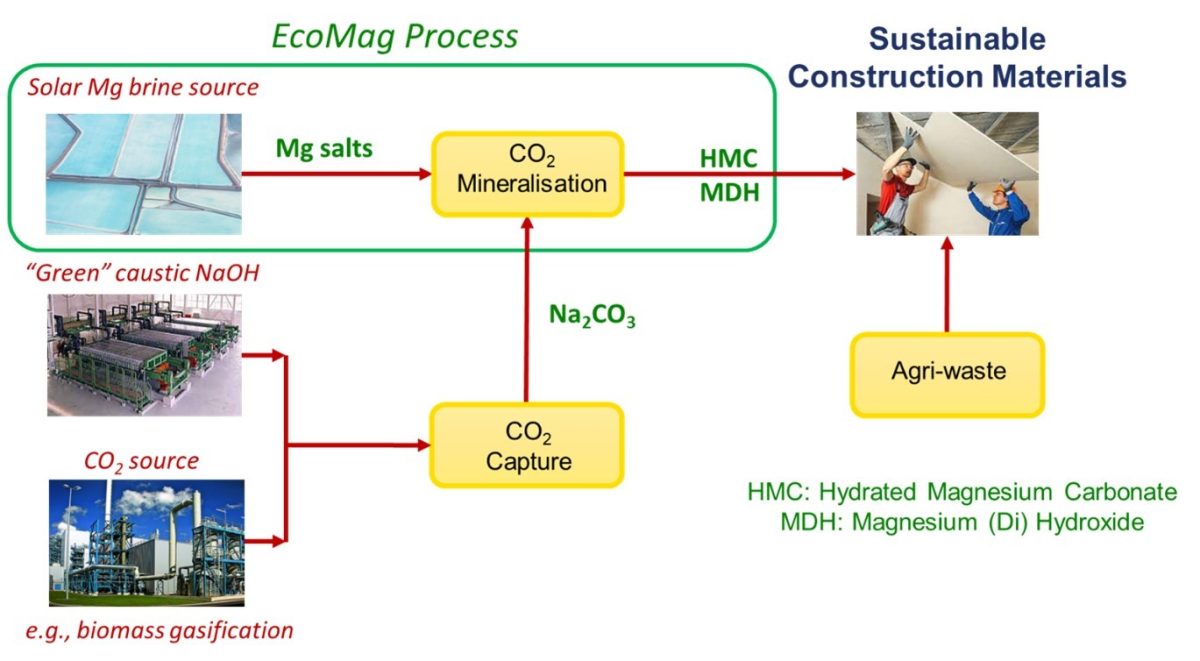
Figure 1 Overview of the EcoMag process to produce hydrated magnesium carbonate (HMC) and magnesium di-hydroxide (MDH) for use in sustainable construction materials. Courtesy of A/Prof. Jason Scott, UNSW
The life-cycle assessment (LCA) of EcoMag’s process was recently completed in consultation with the German Aerospace Centre (DLR).
EcoMag also engaged TÜV SÜD Energietechnik to audit the resulting report to ensure it adhered to ISO 14040 (Environmental management — Life cycle assessment — Principles and framework) and 14044 (Environmental management — Life cycle assessment — Requirements and guidelines).
The LCA indicated that when producing HMC, MDH and MgO in the EcoMag process, the largest carbon footprint originated from the reagent used (NaOH or Na2CO3) for Mg compound recovery (e.g., Figure 2 shows the case where NaOH is the primary reagent), Dr Tim Zurrer, a postdoctoral researcher involved in the project, says.
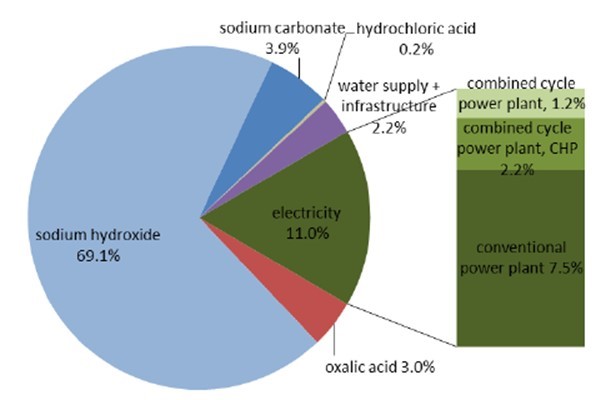
Figure 2. Greenhouse gas emissions of the HMC production process using NaOH as the primary reagent (% CO2eq / kg HMC). Courtesy of A/Prof. Jason Scott, UNSW
Techno-economic (TE) assessment of the EcoMag process, which considered the various process modifications, found that the reagent used (NaOH or Na2CO3) is the largest (60-70%) and most sensitive contributor to total production cost.
“Switching feedstock reagents from Na2CO3 to NaOH introduces an additional cost of $0.10/kg HMC which, according to EcoMag’s market research on the sale price of HMC, can be absorbed without significantly affecting financial returns over the life of the project,” Dr Zurrer explains.
Overall, the study established a roadmap to produce carbon-negative hydrated magnesium carbonate. Switching the feedstock (from Na2CO3 to NaOH) and the fuel source (from natural gas to green hydrogen or electrified heat) make it possible to produce HMC that sequesters CO2 from biomass gasification, as illustrated in Figure 3. The carbon footprint of gypsum plasterboard is provided for comparison.
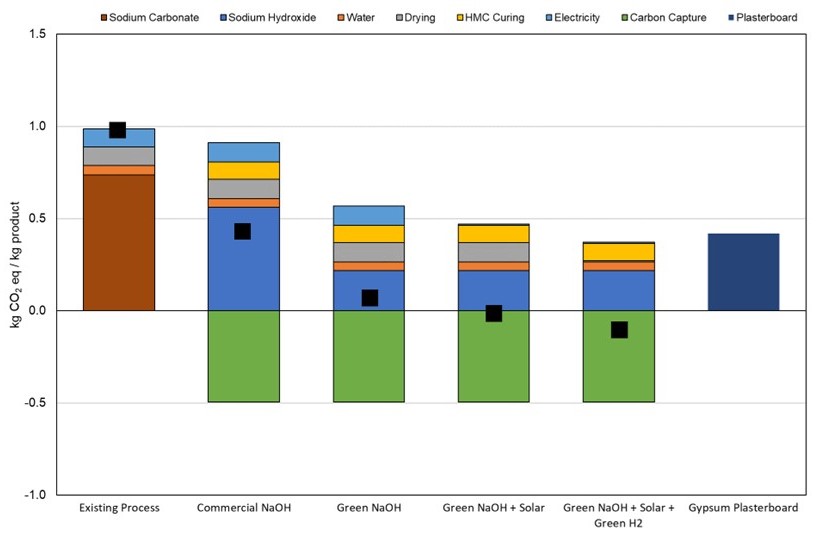
Figure 3. Roadmap to carbon-negative hydrated magnesium carbonate (HMC) with gypsum plasterboard as a comparison. Nesquehonite MgCO3.3H2O used as a basis. Black squares represent Net CO2 emission from the process. Courtesy of A/Prof. Jason Scott, UNSW
Ramping up for production of planet-friendly plasterboard
In preparation for manufacturing trials, EcoMag’s current pilot-scale HMC/MDH production line, located at the company’s Chatswood site, has been retrofitted with CO2 utilisation capability.
“The CO2 sparger components have arrived and been installed in EcoMag’s pilot-scale process at the Chatswood site,” says EcoMag CEO Tony Crimmins. “The unit has been commissioned and produces the required Na2CO3 solution to integrate into EcoMag’s pilot plant.”
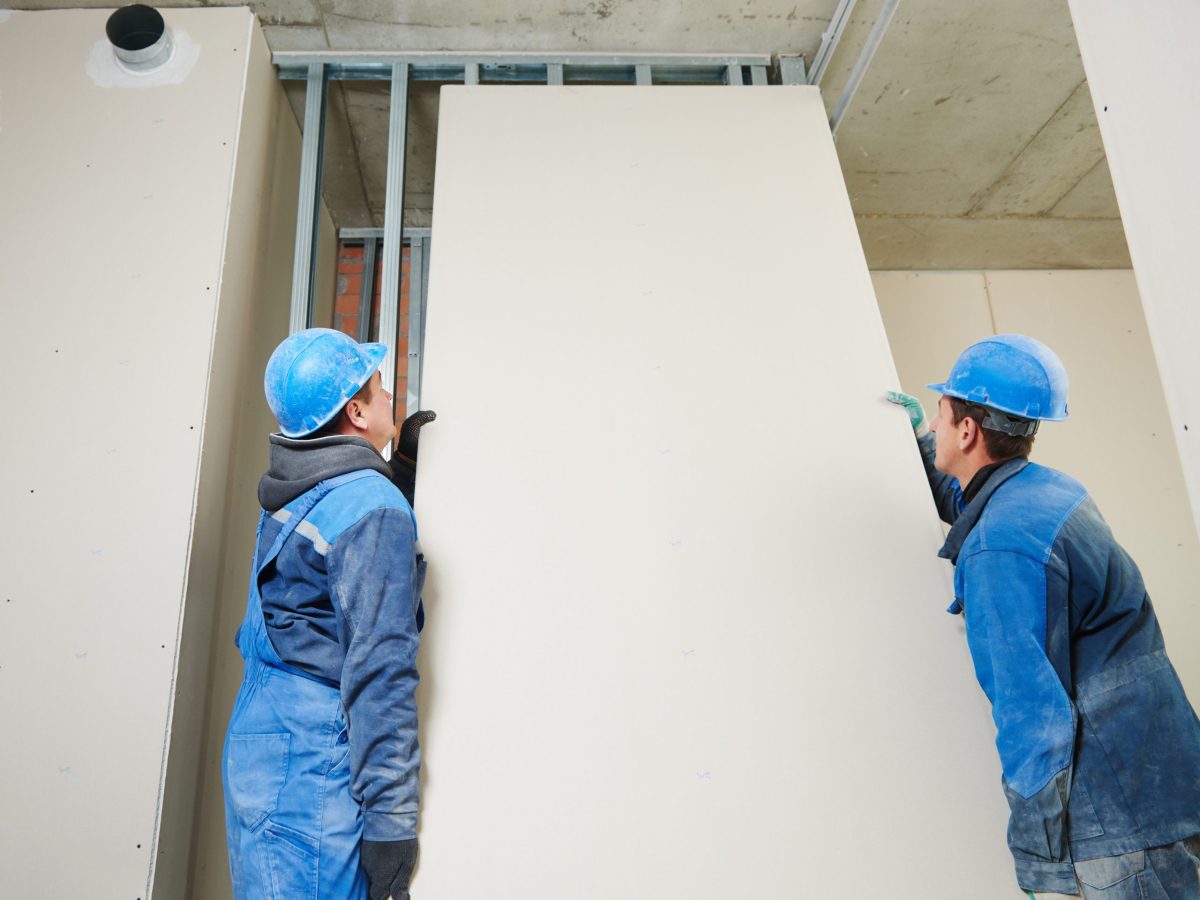
Construction workers position a sheet of plasterboard. Credit: Shutterstock
Fabricating, characterising and optimising sustainable cladding samples
“The chemistry associated with HMC/MDH formation is quite complicated and is considerably influenced by the recovery conditions,” A/Prof. Scott notes. “It is important to understand and optimise these relationships, as the final HMC/MDH characteristics ultimately define the performance of the internal (plasterboard) and external cladding products.
“From a fundamental perspective, Ms Aaron has been acquiring an understanding of the chemistry behind HMC formation, which involves analysing material properties such as surface area, crystal phase and surface/structural chemistry.
“Collating this information will allow us to map the HMC/MDH characteristics with recovery conditions so we can then select the conditions that will give us a final product with the strength, moisture tolerance and flame retarding capabilities necessary for real-world application.”
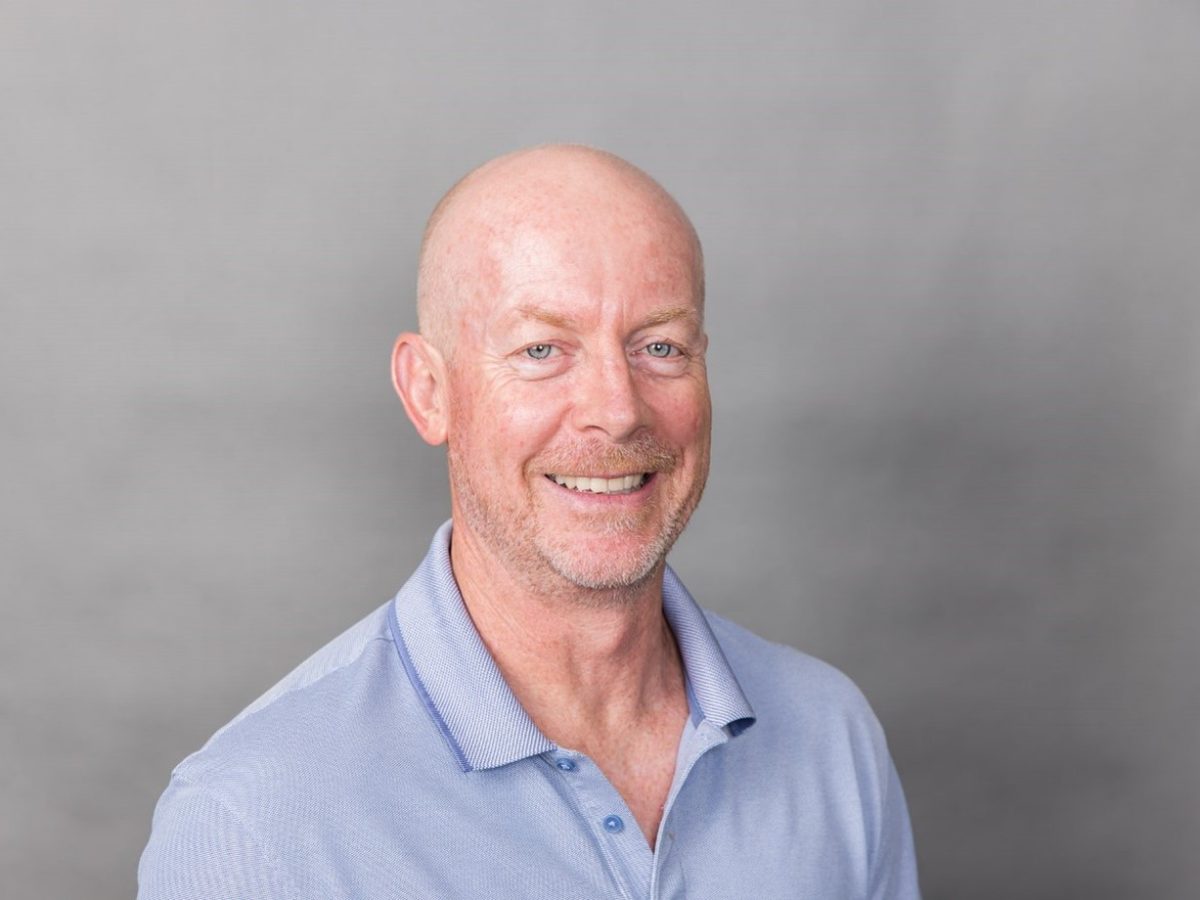
Sustainable composite materials expert and UNSW Associate Professor Jason Scott leads the project team. Credit: UNSW Sydney
The project team
The ‘Agri-food waste CE framework’ project team is led by sustainable composite materials expert, UNSW School of Chemical Engineering Associate Professor and Deputy Lead of the university’s Particles and Catalysis Research Group (PartCat), Jason Scott. The project team includes UNSW Professors Rose Amal, Guan Yeoh and Cordelia Selomulya; Dr Tim Zurrer and Dr Timothy Chen; and FFS PhD Natalie Aaron, with one more PhD to be recruited. EcoMag CEO Tony Crimmins, Chief Technical Officer Dr Tam Tran, Dr Michael Braaksma and Dr Van-Tri Luong also have substantial input into the project.
Lead image: Construction workers install conventionally manufactured plasterboard sheeting. Commercially viable circular-economy-based plasterboard and cladding materials with properties similar to or better than their less sustainable equivalents could dramatically shrink the carbon footprint of the construction industry, across Australia and the world. Credit: Shutterstock